The material handling industry is like every other in the 21st century: forced to do more work with fewer workers and at slimmer margins than ever before. Between staffing shortages and pay increases, and demands to handle ever-increasing volume of product in the same crowded warehouse, facilities managers and CEOs are looking for new solutions.
How are modern warehouse managers able to store and process more inventory with limited staff and finite space? The solution lies in warehouse automation with streamlined processes and better systems that optimize the use of space and allow the current workforce to handle more work.
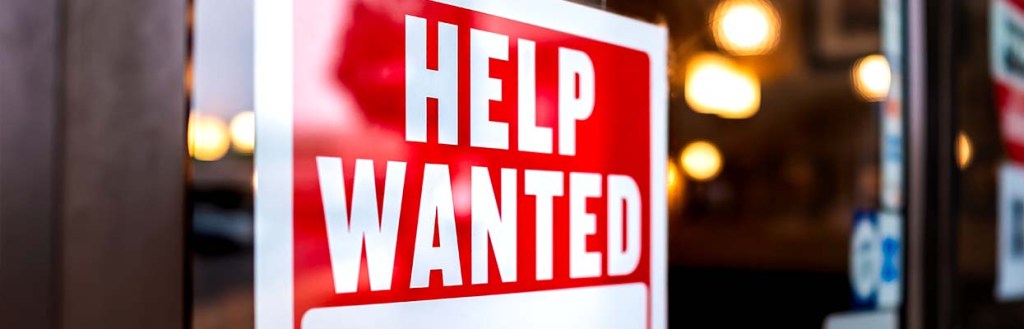
AMRs Reduce the Impact of Worker Shortages
At a time when it’s difficult for warehouse managers to staff to needed levels, Autonomous Mobile Robots bring relief. Material handling robots don’t take days off, call in sick or become less productive because of fatigue. These robots also remain a fixed cost; they don’t ask for pay raises; and there’s no lengthy recruitment and hiring process. When job requirements change, they can be programmed as needed and don’t need to be retrained.
AMR with Casters, Carts and Tuggers
Casters, carts and tuggers have been the backbone of material handling for a long time, but those old standbys are starting to get a little help from AMRs. Platforms on casters are great for moving large loads from one spot to another but have always required an alert, rested human worker. Maneuverability is an issue, as they require wide spaces and don’t handle sharp turns or fast stops very well. Accidents involving tired workers and overloaded casters are common.
Larger AMRs used as tow tractors decrease the reliance on human effort, and decrease the risk of injury and product damage. These robots can tow large loads, and navigate safely and efficiently through crowded facilities.
A material handling robot, on the other hand, can work safely and consistently for an entire shift. AMRs are just as alert on the twentieth load as they are on the first. Continual activity boosts productivity and mitigates the impact of worker shortages.
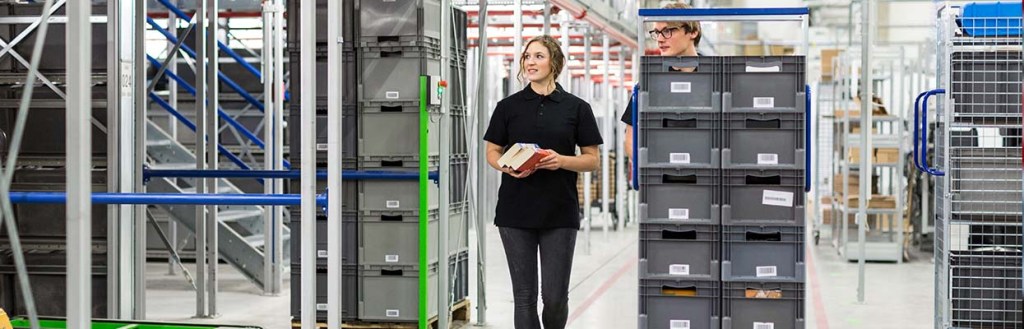
A heavy load resting on casters is an accident risk when human workers are involved, as a shifting load can topple and cause injury or property damage. Robotic carts, such as the GoCart series from Yujin Robot, can stop quickly if another worker steps in front of them, or if they encounter an unexpected obstacle.
Material handlers have used carts to pick and transport orders since the dawn of the industry. When they were introduced, carts solved the obvious problem: workers could only carry so much at one time. However, the limitations of carts are just as obvious. Because of their size, carts can be slow to move and unwieldy to navigate. Aisles must be wide enough to reduce bumps and accidents. Workers spend their time moving material instead of more profitable, more complicated tasks.
Robotic carts, on the other hand, navigate smoothly and autonomously. They glide through tight corridors without a problem, which allows more space to be used for storage. These AMRs are built for stability — they can carry large, heavy objects without tipping.
Tuggers, or tug trains, reduce much of the safety risk of carts and platforms on casters, moving a lot of material. In a tug train, several carts are chained together and pulled by an operator driving a tow vehicle, in the same way an engine pulls a locomotive. These carts, slow moving and low to the ground, are a much safer option than casters, carts or even forklifts. Still, tuggers need to be tugged, and they navigate through a wide path. Turning corners is a challenge, and speed is sacrificed for load size.
Autonomous Mobile Robots solve the same issues a tug train solves, but they do so without the need for a human operator. Where a tugger follows a predetermined path, AMRs use onboard navigation technology to move in the most efficient path.
AMR in a Connected Facility
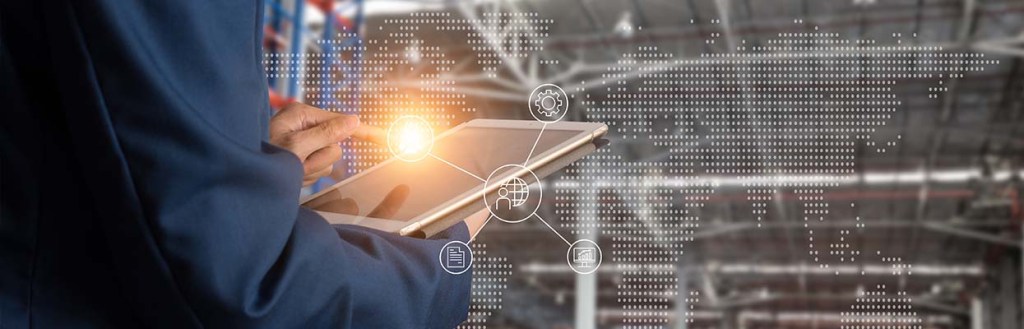
Autonomous Mobile Robots have another advantage over an all-human workforce: They can connect wirelessly with a warehouse’s data streams, and respond quickly to changing needs. Instead of a foreman hunting down a worker to issue new instructions, a warehouse fleet management system can direct every robot to its best use at all times. Robotic carts for material handling integrate seamlessly with automatic doors; in multi-level facilities, they’ll even use an elevator without human intervention.
Billions of pallets are in motion around the world every day, and volume continues to increase. If your workforce struggles to keep up, take comfort in knowing that you’re not alone — and that Autonomous Mobile Robots can help.