The words “automation” and “robotics” can be frightening. Many employees assume that bringing automation to their workplace puts their jobs at risk. Others, including managers and executives, worry that automated systems and mobile robots will harm morale, or force their business into rigid systems that can’t adapt as easily as a human workforce.
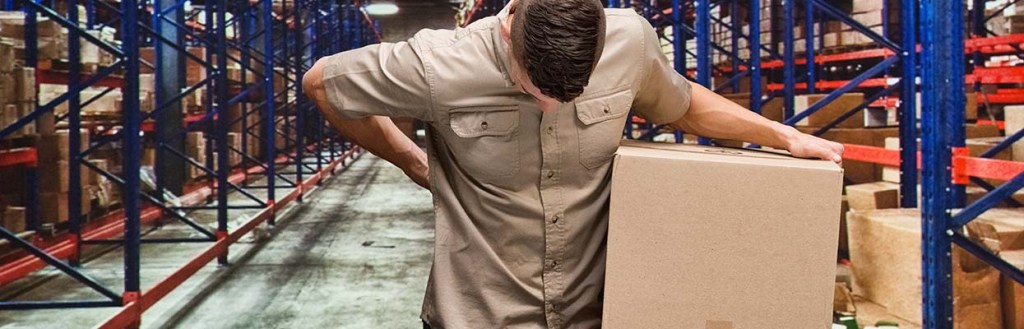
AMRs Improve Workplace Safety
Jobs that include a lot of heavy lifting, bending and squatting have a high incidence of on-the-job injury. Stacking heavy boxes on warehouse shelves can leave workers with joint and back problems brought on by hours of strain. These work-related inuries are painful, and they can take a long time to heal.
Autonomous Mobile Robots, such as Yujin Robot’s GoCart series, handle the heavy lifting and transport with ease. Rather than being subjected to repetitive strain or back pain, workers can focus on less risky, more complicated work. Instead of hurrying from place to place in a busy factory or warehouse, workers can remain safely at their workstations and let the robots make that trip.
One of the most dangerous jobs in a factory or warehouse is that of forklift driver. Forklift accidents cause nearly 35,000 serious injuries and more than 80 deaths per year in the United States alone. The introduction of autonomous forklifts eliminates the risk of serious injury both to the driver and to other workers.
In some settings, such as hospital COVID wards with highly infectious patients, workers are at risk simply by moving from one room to another. Workers faced with the possibility of infection can suffer anxiety and increased job-related burnout.
Even when the risk of infection isn’t a concern, performing mundane tasks such as meal delivery breeds frustration. Registered nurses prefer to spend their time caring for patients rather than serving lunch. Fortunately, mobile robots are taking over these duties at more and more hospitals, leaving healthcare professionals with more time for patients.
AMRs and Job Fulfillment
Two of the biggest morale killers in any job are boredom and a feeling that one’s work isn’t important. Mundane, repetitive tasks leave workers feeling unfulfilled, and they promote high turnover. When these tasks are instead given to mobile robots, employees can be assigned work that challenges them and has a noticeable impact on their business unit.
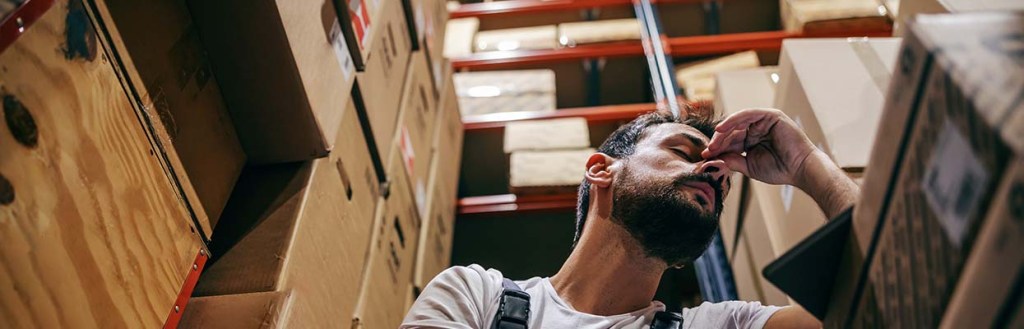
Even workers whose jobs are more complex than stocking shelves or delivering meals can become frustrated with outdated systems or inefficient processes. A warehouse manager who takes pride in his work wants his team to be as productive as possible. It’s unpleasant to push for excellence when you’re saddled with inefficiency and out-of-date methods. On the other hand, a manager who has modern tools such as mobile robots or other automation at his disposal, and who sees the positive results from that technology, has reason to celebrate.
Talk to Your Workers
When you consider whether to bring in an automated warehouse system, start by talking to the humans you already employ. Ask them about their frustrations. Review injury reports, and evaluate how many incidents could have been prevented. Think about the problems you might solve for your staff.
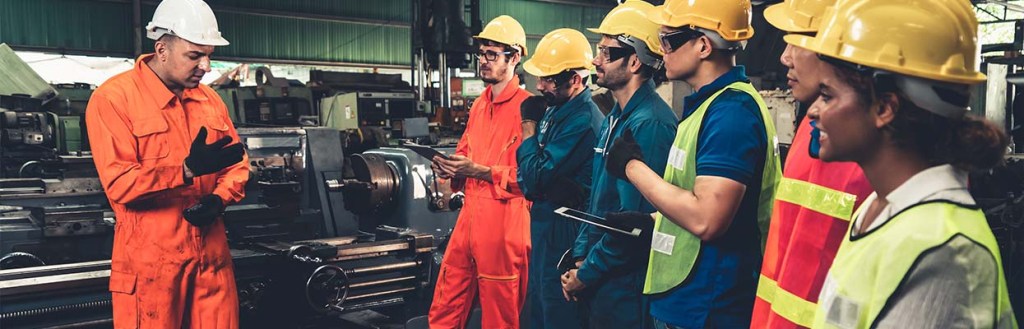
Then, when you introduce the team to its new robotic coworkers, remind them of those frustrations and safety concerns. Show them the way their jobs will be more safe and less stressful. Don’t dismiss their concerns about job loss; assure them that one of the reasons you’ve chosen AMRs is to reduce employee turnover.
Autonomous Mobile Robots are more than just a tool. Managed correctly, they improve the quality of your workers’ lives and give them more time to be creative, innovate and do all the things that humans do best.