Deciding to add robots to your workspace sounds like a no-brainer. Warehouse automation can drive down costs, conserve workspace and preserve materials — all while ramping up productivity and quality.
Warehouse automation has proven effective in our on-demand economy, as Forbes reports that the warehouse robotics space is increasing at a clip of 15% percent per year. Inside its centers across the U.S., retail giant Amazon has more than 200,000 robots — up from the 15,000 it had in 2014 — on hand to make sure its customers receive free one-day shipping on everything from books to bath bombs to batteries.
However, going forward with warehouse robots is a decision that must be made with great care and scrutiny. You’re not necessarily replacing your human workforce — you’re simply enhancing it, so it’s important that your employees don’t feel threatened and learn to embrace rather than resent this addition.
Integrating the wrong machinery into your workplace or not having the full faith of your staff can have devastating effects on everything from your bottom line to company morale to employee safety. So, it’s important to make sure you’re asking the right questions before tackling such an endeavor.
Some things you should consider when integrating into an automated warehouse
Safety
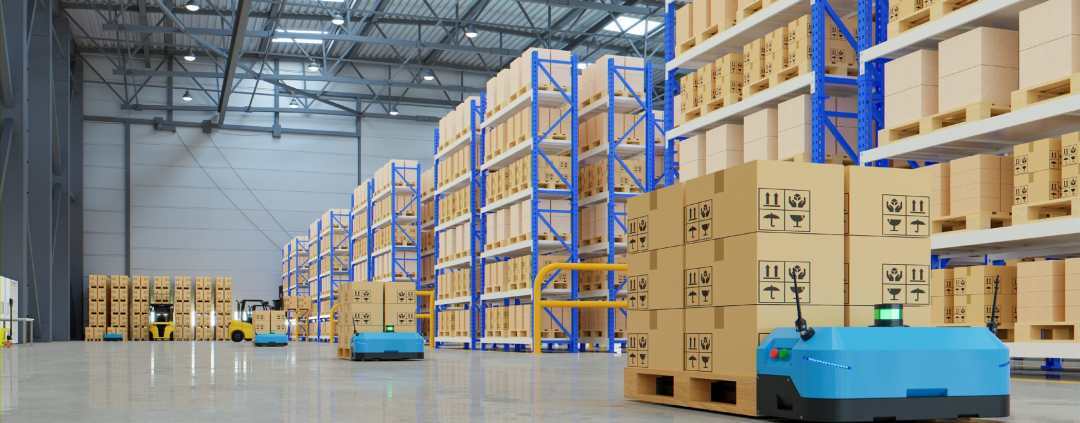
warehouse robot
This trumps all. It’s important to not overwhelm your staff — so if you’re integrating warehouse robots, let your employees know a few weeks, or if possible, months, beforehand. Then spend that time getting your team trained on not only how to use and operate robots, but also how to spot inefficiencies and problems within the machines. It’s also important to study your warehouse to make sure you don’t need to make any alterations or changes before bringing robots into the fold. If your space has elevators, for example, it’s important to find robots who can fit inside and are integrated to allow them access without human assistance. An elevator system, as well as automatic doors, should be compatible with your robot system. And, if your warehouse has lots of obstacles on the floor, it may be necessary to configure the robot’s course so it can navigate the space safely and efficiently or it might be necessary to clean up the floor and remove the obstacles completely.
Once you’ve decided you have the facilities in place and staff on board to begin warehouse automation, the integration should be performed at a slow, gradual pace. Don’t make one huge purchase. Rather, ease your business and companies in, and then if the process is working well, you can add more and more robots to your warehouse weekly or monthly.
Cost
Integrating warehouse automation isn’t cheap, especially if you’re outfitting multiple locations — a mobile robot can cost up to $100,000, and a fixed robot (such as an industrial arm anchored to a specific point) can cost up to $400,000. You need to make sure your return on investment covers the cost, or else you’re wasting resources.
That’s why it is important to pick an autonomous mobile robot (AMR) partner who allows you to customize a plan catered to your specific business needs. Try to find an AMR business with inexpensive upfront and hardware costs that allows you to purchase warehouse robots through a scalable, subscription-based model. That way, you only pay for what you need. And if your needs change from one month to another, so does your cost.
This may take some research and legwork on your part — but it will all be worth it if it helps your business manage costs while increasing profit and productivity.
Your People
When it comes to automation and the effect it will have on your staff, safety is the primary concern — but it isn’t the only one.
According to the U.S. Bureau of Labor Statistics, 2 million people will be working in warehouses by 2030 — a huge jump from 2010 (645,200). Your employees aren’t going anywhere, and it’s up to you to comfort those who may view warehouse automation as a threat or your way of saying they’re not doing the job you need them to do. The onus is then on you to get your employees comfortable working alongside rather than against automation. A good way to accomplish this is to involve them in the decision-making process and keep them informed during every step of the integration process.
Perfection is an illusion, and that goes for automated warehouse robots. No matter the company, the warehouse or the ease of the integration, there will be glitches and malfunctions, especially early in the process. If your employees haven’t bought in to automation, they’ll lose confidence and faith the moment something goes wrong, which will have a devastating effect on company morale and create more headaches than you want to handle.
Explain to your employees that warehouse robots are good for your clients and company, and that a boon in productivity and profitability is good for everyone involved.
The Right Partner
Once you’ve decided on integration, the key is to find the right manufacturer or solution partner. While nothing is cemented as to what makes the perfect AMR partner, there are certain criteria and qualities that may make one manufacturer stand out from another.
You want to choose a company that puts an emphasis on safety and won’t simply shove something down your throat that wouldn’t be a good fit for your warehouse or employees. The right AMR partner will visit your warehouse and give it a thorough evaluation before making any decisions or recommendations.
Credibility and experience are important as well. You want to pick a manufacturer or solution partner that has been dealing in warehouse automation for a number of years and has handled and rolled with the changes that occur in the fast-paced world of robotics and technology. It also helps if the company has experience integrating robots for other companies in your industry — though you should make sure they’re not working with any direct competitors — so they have a feel for what you may need.
Basically, you want someone you can trust.
At Yunjin Robot, we specialize in robotization that is safe, time-tested and empowering. We offer cost-effective custom packages, backed by extensive research and development, and all of our robots are field-tested, efficient and safety ready..
Learn more by downloading our free white paper.