Autonomous Mobile Robots (AMR) have brought a new level of automation to the internal logistics of manufacturers, retailers and other types of businesses.
Unlike AGVs (Automated Guided Vehicles), AMR can trace their route without the need of magnetic tapes, permanent tracks or any type of tethering. AMR have more freedom, and navigate to the best route. Think of the difference between a train and an automobile; a train’s movement is limited to its predetermined path, while an automobile may change direction as needed.
When operating in an unknown environment, AMRs use SLAM (Simultaneous Localization and Mapping) technology to scan the surroundings, build a virtual map and, at the same time, navigate through it safely. The environment data is constantly updated to allow the vehicle to recognize and avoid any new obstacles, such as moving objects and people.
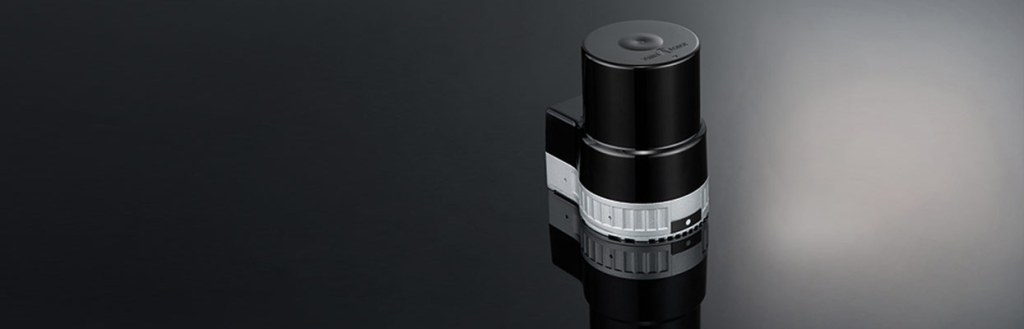
SLAM technology typically uses visual sensors and/or LiDAR (Light Detection and Ranging) to identify nearby objects and surroundings. LiDAR creates a 2D or 3D map by measuring the reflection of pulsed light on objects. Visual sensors use one or more cameras to acquire successive frames of the environment and perform 3D feature-point triangulation. Robots use SLAM the same way humans use the part of the brain that understands place and movement, creating a mental map of the environment. LiDAR provides data for SLAM the way your eyes provide images to your brain, helping you recognize objects around you.

5 Ways AMR Can Benefit Your Company
Simultaneous Localization and Mapping, or SLAM, offers a helping hand to AGV manufacturers. With SLAM robotics te
The use of fully or semi-automated vehicles is often associated with large plants with several production lines— such as those of car manufacturers — or logistic hubs.
In fact, AMR can also be implemented successfully by smaller manufacturers and retailers, and any other company where internal logistics take up considerable resources, such as healthcare providers.
There are five main reasons for that.
1. They’re scalable and easier to implement.
Unlike AGVs, autonomous mobile robots require no guiding infrastructure and can operate with no extensive training or programming experience; they’re also scalable. Businesses with limited needs can start with just a few units — with a smaller investment and faster implementation — and then scale with time. If at any point the company needs to move to a bigger facility, the ATS can be moved and set up quickly.
2. They adapt easily to smaller environments.
Warehouses can be crowded places, with narrow aisles, pallets of product as obstacles blocking paths, and workers scurrying from place to place. Since they don’t rely on a fixed navigation path, Autonomous Mobile Robots move easily in smaller facilities with narrow corridors and less than optimal layouts. While AGVs simply stop whenever they encounter an obstacle and resume movement when the path is clear, AMRs can move around objects, use elevators and go through automatic doors.
3. They improve efficiency.
Human beings have limited capacity for physical labor. Lifting and carrying heavy materials causes fatigue, and sometimes injury. Wheeled push carts were the first step to solving this problem, but products can be spilled and inattentive workers sometimes injure their coworkers or break merchandise.
AMRs need to recharge every now and then, but they don’t strain muscles, hurt their backs, or injure workers through carelessness. Warehouse automation and automated material handling and storage systems speed up operations and allow more time for skilled employees to do valuable work. Retailers and manufacturers can fulfill orders more quickly, while hospitals can deliver samples to labs or medications to patients without delays.
4. They reduce cost related to automation and poor quality.
Autonomous Mobile Robots typically require lower maintenance and training cost than human workers. Once AMR are installed and programmed, they are ready to operate and don’t require additional training. They perform repetitive tasks more accurately and more quickly than human workers. They also lead to fewer errors, reducing the cost of poor quality.
5. They make the workplace safer.
Automated material handling and storage systems require less manual input to operate, so they’re equipped with more safety mechanisms. This is particularly important for warehouses and production environments with many unpredictable obstacles, or where hazardous materials are to be transported. Yujin Robot’s systems conform to the strictest ISO13482 safety standards.
Two Use Cases for ATS
The use case for hospitals is particularly useful to show the versatility of Autonomous Mobile Platforms. Yujin Robot is currently working with Sumetzberger, an AMR systems integrator based in Austria, to deploy an AMR solution at a Slovenian hospital.
The requirement of the facility was to deliver medications from the pharmacy located in the basement of a new hospital building to the COVID-19 unit located on the third floor of an old building. Multiple daily trips from one point to the other took up a considerable amount of hospital staff time, and repeated exposure to COVID-19 patients posed health risk to staff.
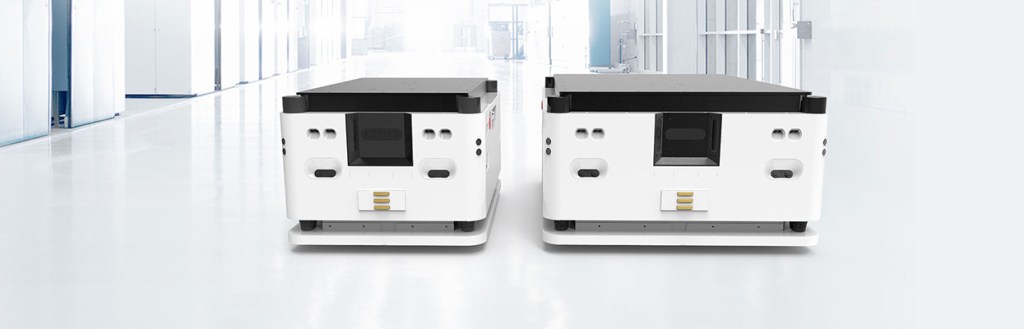
The solution was Yujin Robot’s GoCart250, an autonomous vehicle that can carry loads up to 250Kg on a flat surface and travel easily from one building to the other and through narrow corridors, thanks to its relatively small size (924 mm x 724 mm x 420 mm). Yujin’s FMS (Fleet Management System) integrated with PLC (Programmable Logic Controllers) system allows the robot to go into elevators and through automatic doors. It features two 3D LiDAR sensors for navigation and three 2D LiDARs ultrasonic sensors and cliff sensors for obstacle detection and additional safety.
Yujin Robot and Sumetzberger will be deploying similar solutions at other hospitals in Austria and other European countries, which needed a general delivery system for general supplies, lab samples, food, sterilized goods etc..
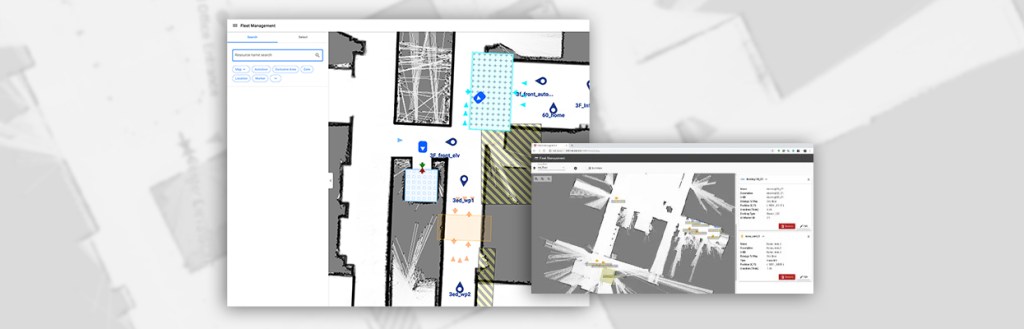
For all solutions, each Autonomous Mobile Robot is controlled and monitored by a Fleet Management System (FMS). The FMS runs on a server and acts as a centralized decision maker. It controls traffic and can communicate with the warehouse automation system, WMS (Warehouse Management System), MES (Manufacturing Execution System), EMR (Electronic Medical Records) or other management system at the facility.
Accessible Automation
Retail and manufacturing businesses of all sizes are facing increased pressure from their customers — whether they be consumers or other businesses — who expect orders to be fulfilled on schedule and flawlessly. At the same time, the COVID-19 pandemic stretched many healthcare facilities to their limits, highlighting how improved efficiency can effectively save more lives.